Selecting Oil for Hypoid Gears Under Extreme Load Conditions
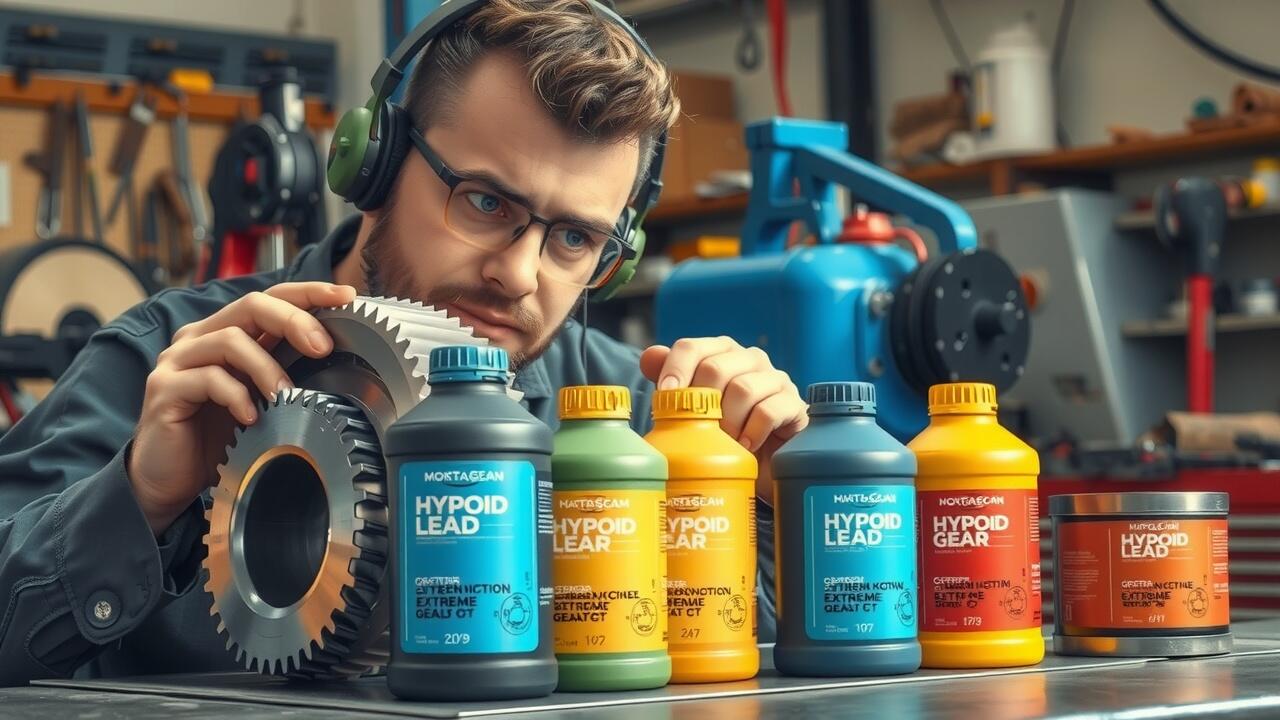
Key Takeaways
- Assessing lubricant effectiveness in hypoid gear arrangements
- Heat regulation and its influence on lubricant choice
- Frequent misunderstandings regarding gear lubricant
- Optimal upkeep strategies for hypoid gear lubricant
- Illustrative examples: Effective lubricant choice in severe environments
Monitoring Oil Performance in Hypoid Gear Systems
Effective monitoring of oil performance in hypoid gear systems is crucial for maintaining operational efficiency. Regular viscosity checks reveal changes in gear oil properties due to thermal stress or contamination. For example, gear oil that starts with a viscosity grade of ISO VG 680 may degrade to a lower grade under extreme conditions, impacting load-carrying capacity. Industry standards recommend performing viscosity tests at least every three months or after significant operational cycles. This proactive approach enables early detection of oil degradation.
The presence of particulate matter is another critical factor in assessing gearbox lubrication. Use of particle counters can provide quantitative data about contaminants, allowing for targeted filtration strategies. A study showed that a reduction in wear particles by 20% enhanced the lifespan of gear box oil significantly, thus proving the link between particulate matter levels and oil performance. Regular sampling and analysis of gear oil lead to informed decision-making regarding oil changes, ultimately resulting in minimized downtime and maintenance costs.
What Signs Indicate Oil Degradation? (Key Indicators to Watch For)
Monitoring the condition of gear oil is critical for maintaining the performance of hypoid gear systems. Oil contamination can manifest as color changes, often shifting to a darker hue due to the presence of particulate matter or thermal breakdown products. Additionally, viscosity alterations may indicate that the oil has lost its lubricating properties. For instance, significant deviations from the standard viscosity grade can compromise the gearbox lubrication efficiency, increasing wear rates and potential gear failure.
The presence of metallic particles within the oil serves as a warning sign of internal wear patterns. Tools like oil analysis can quantify the size and concentration of these particles, providing insights into impending maintenance needs. Regular monitoring should include checking for abnormal odors, which can signal chemical breakdown, and performing periodic fluid analysis to measure acidity and oxidation levels. Adopting a routine for assessing gear box oil not only preserves the integrity of the gear system but also optimizes operational lifespan under extreme load conditions.
Temperature Management and Its Impact on Oil Selection
Temperature plays a critical role in the performance of gear oil, influencing both viscosity and protective properties. For instance, a standard synthetic gear oil has a viscosity index (VI) that indicates its ability to maintain stable performance across temperature variations. In cases where temperatures exceed 200°F, low-viscosity oils can thin excessively, risking compromised lubrication in hypoid gear systems. Conversely, high-viscosity oils may not flow adequately at lower temperatures, leading to wear and tear on components during startup conditions. Adhering to the manufacturer’s specifications for operating temperature is essential for ensuring optimal gearbox lubrication and maintaining mechanical integrity.
Effective thermal management requires appropriate selection and monitoring of gear oil under extreme operational conditions. For example, rigorous testing has shown that using a thermally stable base oil, such as ester-based formulations, significantly enhances the oil's performance when exposed to high pressure and temperature. A case study demonstrated that applying a specialized synthetic gear oil in industrial gearboxes running at temperatures consistently above 250°F reduced wear by 30% over a standard mineral oil alternative. This technical insight emphasizes the necessity of considering thermal behaviors for optimal gear box oil selection to extend the life of both the lubricant and the mechanical systems it serves.
Why Is Temperature Control Crucial for Gear Oil Performance? (Thermal Effects)
Temperature control plays a pivotal role in maintaining the integrity of gear oil performance, particularly under extreme loading conditions. Elevated temperatures can accelerate the degradation process of gear oil, leading to a decrease in its viscosity index and a breakdown of its protective additives. For instance, synthetic oils may retain their performance up to 15% longer in high heat compared to conventional oils, but only if managed appropriately. Ensuring that oil remains within the optimal temperature range helps prevent oxidation and formation of sludge, which can impair lubrication capabilities.
Moreover, the viscosity of gearbox lubrication directly affects the load-carrying capacity and overall efficiency of hypoid gear systems. When temperatures rise beyond recommended limits, oil thins out, reducing its ability to maintain a lubricating film. Data from industry studies indicate that gear oil viscosity can drop by as much as 50% when exposed to excessive heat. This loss can lead to increased friction, wear, and potential gear failure, ultimately affecting operational reliability. Regular monitoring of operating temperatures and timely oil changes are vital strategies for mitigating these risks and prolonging the life of lubricants in high-performance applications.
Common Misconceptions About Gear Oil
Misunderstandings surrounding gear oil often lead to suboptimal performance and reduced lifespan of hypoid gear systems. One prevailing myth suggests that all gear oils provide equivalent performance, ignoring the significance of viscosity and additives tailored for specific applications. A study conducted by the American Gear Manufacturers Association demonstrated that using the appropriate oil can enhance gear efficiency by up to 15%, emphasizing the critical role of selecting the right formulation based on operational demands.
Another common misconception is that higher viscosity oils are always superior for load-bearing applications. This assumption fails to account for the balance between protection and flow characteristics essential for optimal gearbox lubrication. For instance, using a 75W-90 oil instead of a 90W-140 may yield better results in high-speed applications, where fluid dynamics significantly impact lubrication efficiency and prevent wear. Selecting the correct viscosity is paramount, as improper choices can lead to excess heat generation and reduced protective properties, ultimately compromising gear performance and longevity.
What Myths About Hypoid Gear Oil Should You Avoid? (Clearing Up Confusion)
Misconceptions about gear oil often undermine the performance and longevity of hypoid gear systems. A prevalent myth is that all gear oils are interchangeable, leading to inappropriate oil selection for specific applications. For instance, hypoid gears, which are commonly used in automotive differentials, require oil with specialized additives to withstand high pressures and reduce wear. This specificity is crucial, as using standard gearbox lubrication could lead to premature failure and costly repairs— a risk that can be mitigated by adhering to manufacturer recommendations and industry standards.
Another common misconception is that higher viscosity means better protection. While viscosity plays a role in lubrication, it does not directly correlate with improved performance under extreme conditions. In fact, using excessively thick gear box oil in cold environments can inhibit proper flow and create increased drag. Research indicates that sticking to the viscosity grades recommended by the American Petroleum Institute (API) enhances overall gear performance and extends oil life, thereby ensuring optimal gear functionality under challenging conditions. Understanding these myths enables technicians to make informed decisions and improve the reliability of their gear systems.
Maintenance Best Practices for Hypoid Gear Oil
Regular monitoring of hypoid gear oil can significantly extend its service life and ensure optimal performance under extreme loads. Conducting routine inspections of oil condition, including viscosity analysis and particle contamination checks, can help identify degradation early. The American Gear Manufacturers Association (AGMA) recommends oil changes at intervals ranging from 1,500 to 5,000 operating hours for hypoid gear systems, depending on the workload and environmental conditions. Implementing a rigorous sampling and analysis program allows maintenance teams to predict when maintenance is required, thus preventing failures and prolonging gearbox lubrication life.
Effective maintenance practices should also include managing oil temperature within specified limits. Gearbox operation tends to generate heat, which can lead to accelerated oil breakdown if not controlled. Utilizing temperature monitoring systems provides critical data for assessing oil performance and adjusting cooling measures accordingly. For instance, maintaining oil temperatures below 200 degrees Fahrenheit can prevent viscosity loss and maintain lubricity. Adhering to manufacturer specifications for the oil type and viscosity grade is essential, as deviations can compromise performance. Regularly scheduled maintenance, combined with accurate temperature control, assures the hypoid gear system operates efficiently at maximum load capacity.
How Can Regular Maintenance Extend Oil Life? (Essential Maintenance Tips)
Regular maintenance significantly enhances the lifespan of gear oil in hypoid gear systems. For instance, adhering to an oil sampling regimen enables operators to detect contaminants and chemical alterations before they escalate into severe issues. Implementing an oil filtration system can further reduce particle contamination, promoting optimal gearbox lubrication while preventing wear on gear teeth. Manufacturers typically recommend changing the gear oil every 1,000 to 2,500 hours of operation, depending on load and environmental conditions, to maximize performance.
Monitoring the properties of gearbox oil, including viscosity and additives, allows for timely interventions. Techniques such as thermal imaging can reveal hotspots indicating friction irregularities or inadequate lubrication. Keeping a log of oil condition can identify trends over time, assisting in fine-tuning maintenance schedules. Regularly scheduled inspections not only enhance machinery reliability but also provide significant savings through reduced downtime and repair costs, thereby establishing a proactive approach to gear health management.
Case Studies
Hypoid gear systems in heavy machinery often face extreme conditions that necessitate careful selection of gear oil to ensure optimal performance. One example is a mining operation where a specific gearbox was subjected to consistent heavy loads and temperatures exceeding 200°F. The lubricants initially employed exhibited significant degradation after only 200 operating hours, leading to increased wear and reduced efficiency. After a period of analysis, the team shifted to a synthetic gearbox lubrication solution specifically engineered for high-load scenarios, resulting in a dramatic improvement in longevity and performance, with oil change intervals extending to over 600 hours without compromise.
Another case demonstrated the effects of oil selection in highly demanding automotive applications. A manufacturer utilized traditional mineral-based gear box oil in their hypoid gears designed for high-torque applications. While initial performance met expectations, wear particle analysis revealed that the gear oil lost its protective properties after 1500 miles, prompting premature mechanical failure. Replacing the oil with a high-quality synthetic lubricant formulated for hypoid applications not only improved gear protection but also reduced operating temperatures by 10%. This shift resulted in enhanced efficiency and significantly longer service life for the gear components, ultimately allowing the manufacturer to achieve rigorous performance standards consistently.
FAQS
What type of oil is best for hypoid gears operating under extreme load conditions?
The best oil for hypoid gears under extreme load conditions typically includes high-quality synthetic oils or those specifically formulated with extreme pressure (EP) additives to enhance protection and performance.
How can I monitor the performance of oil in my hypoid gear system?
You can monitor oil performance by regularly checking for signs of degradation, such as changes in viscosity, color, or the presence of metal particles, and conducting periodic oil analysis.
Why is temperature control important when selecting gear oil?
Temperature control is crucial because excessive heat can degrade oil quality, leading to reduced lubrication effectiveness, increased wear, and ultimately gear failure. Selecting oil with a suitable viscosity for the operating temperature range is essential.
What are some common misconceptions about hypoid gear oil?
Common misconceptions include the belief that all gear oils are the same and that higher viscosity oils always provide better protection. It's important to choose oil based on specific gear requirements and operating conditions.
How often should hypoid gear oil be changed to ensure optimal performance?
The frequency of oil changes depends on several factors, including operating conditions, load, and manufacturer recommendations. Generally, it is advisable to change the oil based on scheduled intervals or when monitoring indicates degradation.